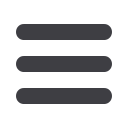
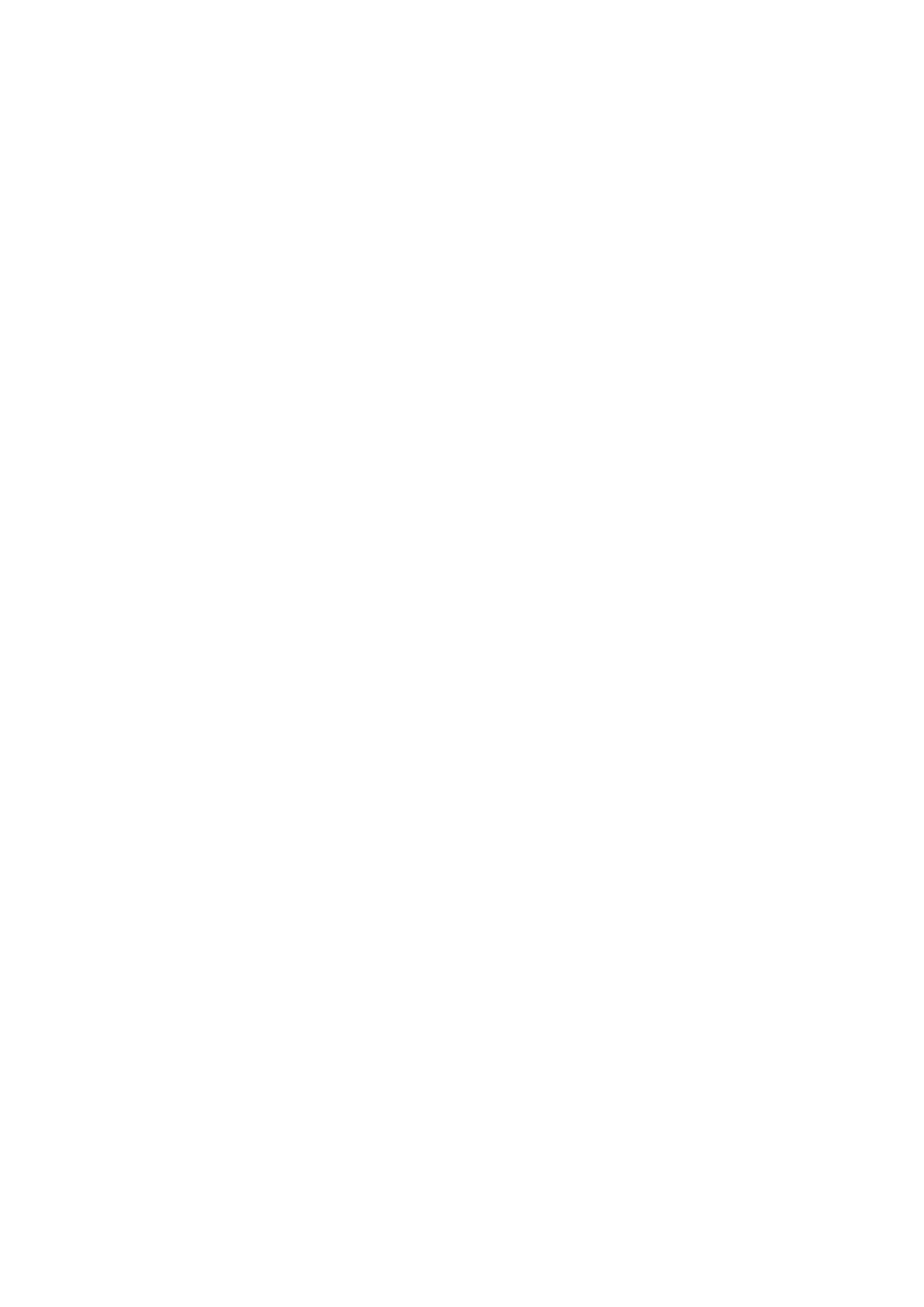
Technical White Paper – Fieldbus Testing with Online Physical Layer Diagnostics
02 / 13
www.pepperl-fuchs.com1
Introduction
Many of the major projects are using digital fieldbus technology as the preferred platform
for control and instrumentation. Most of the lessons learned from the early projects have
been implemented successfully in technology, products and working procedures for the
current projects. Testing the installation as described in working guidelines, published
previously by the Fieldbus Foundation and PROFIBUS International [1], is manual, labor
intensive and requires specialist knowledge.
With the introduction of online advanced physical layer diagnos-
tic (APLD) equipment, fully automated network testing and re-
porting reduces the time and cost for commissioning and plant
upkeep. This technology optimizes the test process and report
generation. At the same time APLD helps establish the optimal
fieldbus installation quality and thus a highly available automa-
tion system. The new APLD equipment needs a revised, yet
vastly simplified construction and commissioning procedure,
requiring minimal technical expertise.
Advanced physical layer diagnostics enable high-speed auto-
mated construction as well as commissioning testing with au-
tomated test report generation and documentation. APLD pro-
vide the ‘handover’ of a system that will have been fully
checked to a highly detailed technical level. This is impossible
to achieve with methods of manual inspection, thus assuring
uncompromised segment quality and system availability for the
end customer and plant operator.
This paper addresses two audiences: For practitioners, it pro-
vides insight into contemporary fieldbus commissioning and
maintenance procedures (chapter
s 2and 0). Step by step in-
structions assist in optimizing working procedures. Decision
makers are presented with arguments and a case study (chap-
ter 4) that show how CAPEX and OPEX savings that are real-
ized with these procedures. Chapter 5 summarizes the facts.
2
Testing and commissioning procedures
This chapter describes testing procedures and improvements that are achieved in the
past years. Testing installations with 4…20 mA interfacing is well-known in practice and
thus not described in detail. Table 2 provides a comparison of basic testing attributes as
they apply to testing the fieldbus installation. This chapter describes how automated
testing utilizing APLD significantly reduces commissioning, testing and troubleshooting
effort in comparison to manual inspection. Savings are even more dramatic in compari-
son to 4…20 mA infrastructures. At the same time the test quality is improved.
2.1
Manual inspection
AG-181 is the working guideline created by fieldbus users and
issued by the Fieldbus Foundation [2]. The versions up to 3.0
(01/2009) detail manual procedures for installing and commis-
sioning fieldbus segments. Manual inspection requires handling
of diverse pieces of equipment such as:
1. Digital multi-meter for current, voltage and resistance
2. Advanced capacitance meter capable of independent
RC measurement
3. Digital storage oscilloscope
4. Handheld fieldbus signal generator and data analyzer
5. Screwdriver for connect and disconnect of devices and
wiring interfaces
6. Set of paper test sheets and pens for manual docu-
mentation
The manual inspection prescribes to first run a check on the
segment cable and then connect each instrument in sequence
and check as shown in Figure 1. Each instrument must be dis-
connected to repeat this procedure for the next instrument.