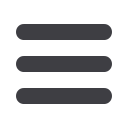
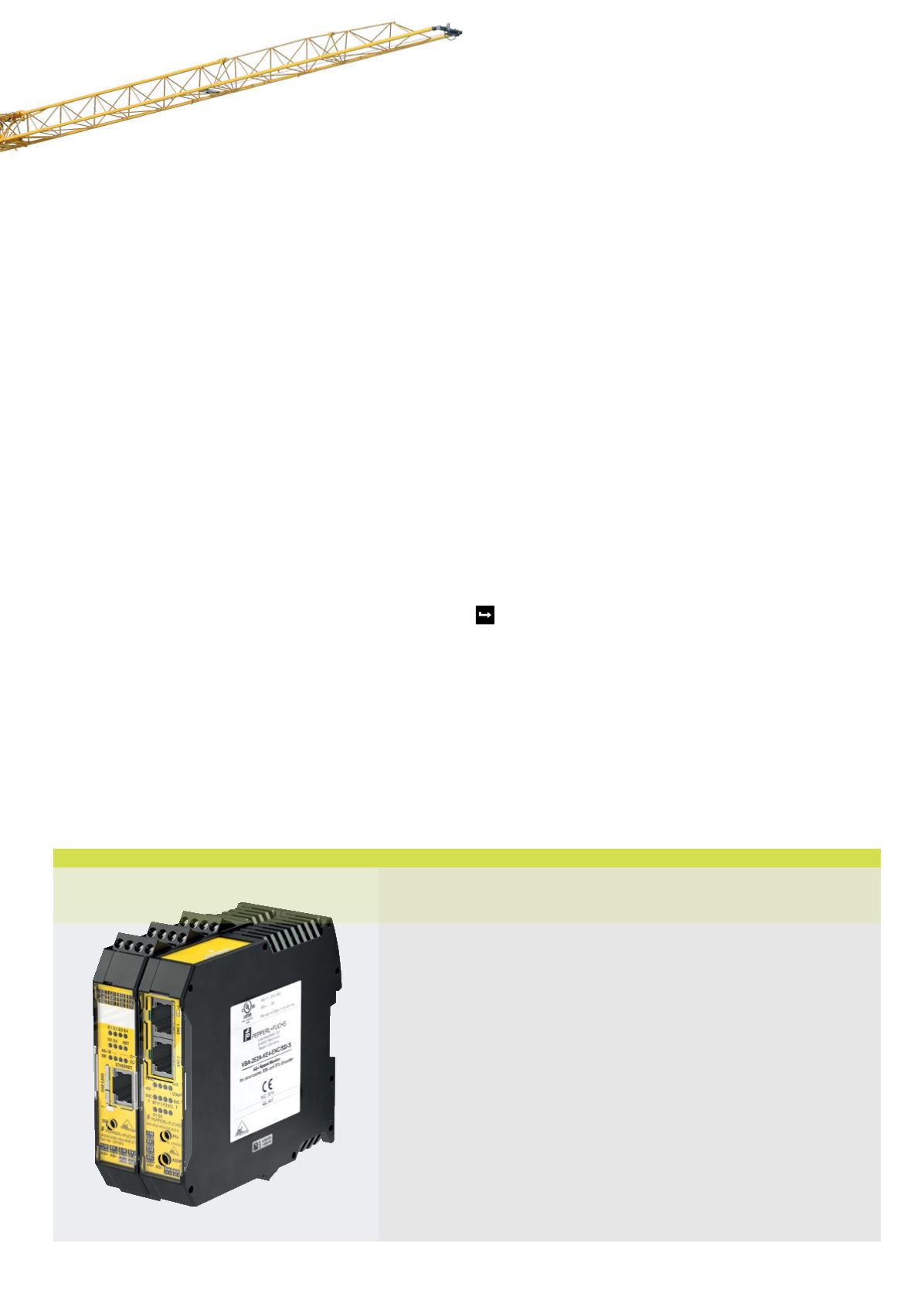
AS-Interface
AS-Interface replaces the conventional wiring technology on the sensor-
actuator level. It has established itself as the standard for cost-effective
signal transmission using the same cable for power and signals. World
wide, there are 35 million installed AS-Interface I/O devices/modules in
use, of which more than three million are safe I/O devices/modules. This
makes AS-Interface the leader among safe field communication systems.
Modules are always installed in the same manner, regardless of the con-
troller and higher-level fieldbus system: The module is placed on the flat
cable at any position and can be integrated in all common controllers.
Machinery and plant manufacturers can completely decouple the installa-
tion from the higher-level controller, which is to be connected later on.
This enables efficient production standards to be defined.
Up to PL e and SIL 3
How exactly is the KE4 used? The module has two inputs for rotary
encoders or linear measuring sensors that can be connected via a
TTL, SSI, or sin/cos interface. Two safe outputs and numerous safety
functions mean that the module can be used in safety-critical
applications. With paired encoders or with one safe encoder per axis
of rotation, the module satisfies the requirements of safety levels PL e
and SIL 3.
Pepperl+Fuchs offers a wide range of different products and technolo-
gies that can be connected to the KE4 module for positioning tasks.
These range from optical distance sensors such as the VDM100 –
which uses Pulse Ranging Technology – to rotary encoders and
even positioning via Data Matrix codes, as is done with the PCV, for
example.
Clear Safety Logic
Not only is the KE4 module able to control and monitor individual
machines and plant components; when used in combination with the
Safety Monitor, it offers a compact solution and can do much more:
“With the monitor, the user has the opportunity to monitor safe position
ranges and speeds from a remote location,” explains Kern. Eight
logical trip circuits offer a wide range of safety options. Safe position
ranges and speeds are parameterized using PC software, and the
configuration is stored on a memory card in the device. “This is a further
advantage: components can be replaced quickly and easily, reparame-
terization is not required,” says Kern. “This means that the safety logic
remains clear and decentralized even for larger and more complex
applications. This often means that a higher-level PLC is not required.”
The AS-Interface network enables flexible expansion of the compact
safety system without being restricted to any particular topology.
n
www.pepperl-fuchs.com/news-as-interface
11