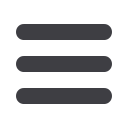
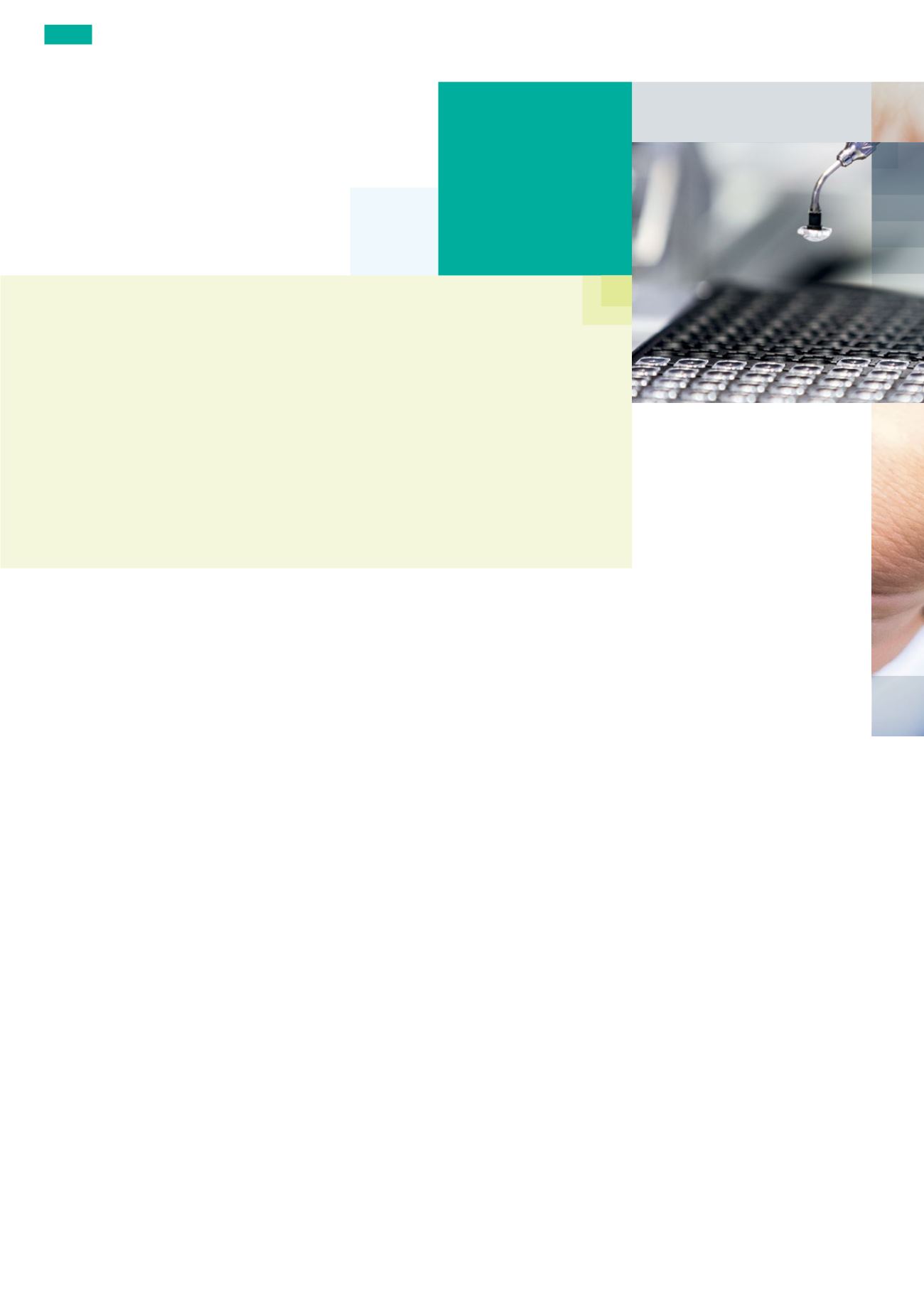
Organs of
perception for
Industry 4.0
Paving the way for Industry 4.0 – this is how Pepperl+Fuchs understands Sensorik4.0
®
.
But it is more than just a theory: The company has already tested practical applications
in its own production plants as well as with other companies. For the future, one thing is
crucial: cross-border, global thinking – and cooperation between automation, mechanical
engineering, and IT.
Individual products that navigate themselves independently through
production and have a role in determining their manufacturing route.
Machines and workpieces that communicate with each other via the
cloud. Transport systems weighing tons that guide themselves driver-
less through factory buildings. Such scenes are no longer the stuff
of an author’s vivid imagination, they are being tested in reality. The
fourth industrial revolution keeps marching on and is changing com-
panies worldwide. This is because companies find themselves facing
new requirements and have to rethink their products, as well as their
production processes, to prepare for the future.
“Today’s sensors provide analog and digital measurements, which are
used for monitoring and controlling as well as in closed-loop control
circuits with high dynamic requirements. In contrast, the sensors of
the fourth industrial revolution – Sensorik4.0
®
– will be one of the
most important data sources for Industry 4.0 concepts,” explains
Dr. Gunther Kegel, CEO of Pepperl+Fuchs. It is important for globally
operating enterprises that the Sensorik4.0
®
concept is tested in
practice. “Together with other companies, we are already testing
practical implementations. But even within our own organization, we
are not standing still: Ultimately, we must prepare our company for
the future and can already benefit from networked production today,”
says Dr. Kegel.
Smart Factory – Smart Business – Smart Product
One example of a good first approach is the horizontally and vertically
networked manufacturing process for the photoelectric R100, R101,
and R103 series in the Pepperl+Fuchs plant in Berlin. Vertical networking,
which means networking of various IT systems on different hierarchical
levels inside a production plant – from the actuator and sensor level, to
the process and production control layer, to the MES and the enter-
prise level – offers many advantages. “The fixed process flow is a thing
of the past – today many different products are manufactured flexibly
according to particular configuration rules,” explains Hinrik Weber,
Head of the Photoelectric Business Unit.
x
Focus
x Technologies + Products
| News for Factory Automation 1/2016
Focus
04